How IoT is changing prototyping
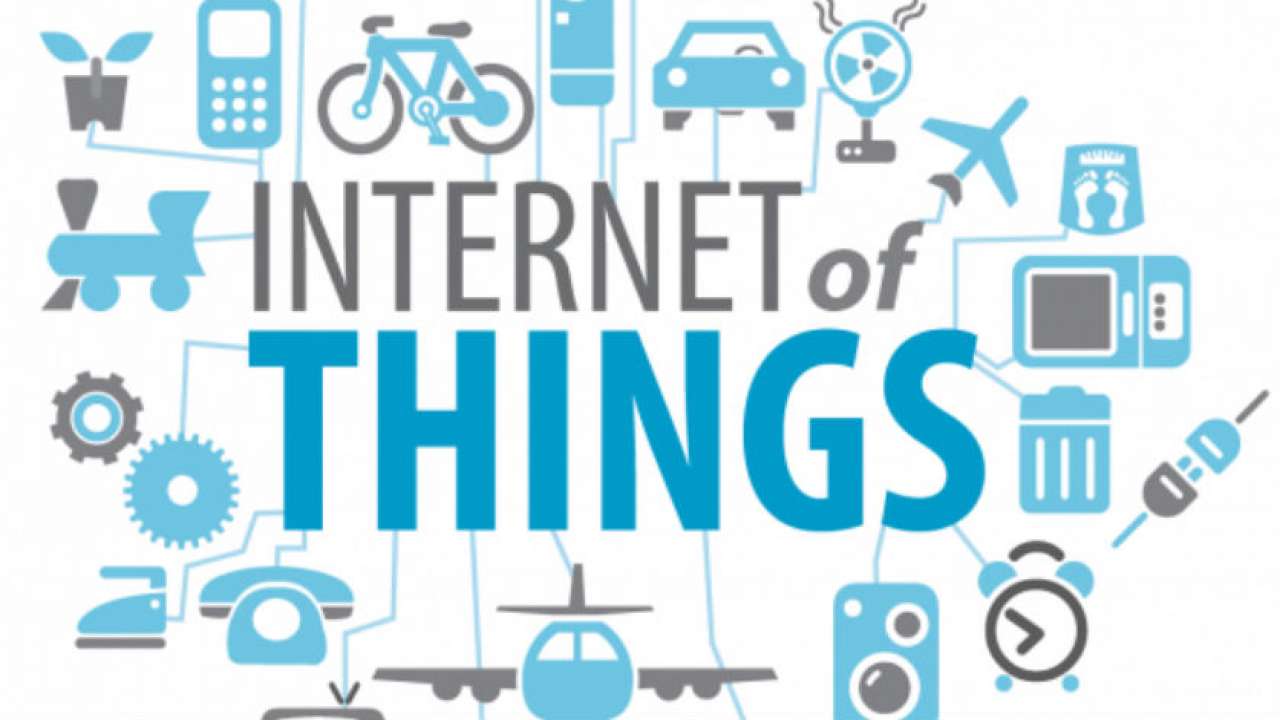
In 1995, a New York Times article by James Gleick offered a glimpse at the future of the Internet of Things by focusing on a hot tub located in Ypsilanti, Michigan. Paul Haas, a pioneer in connecting machines and systems to the burgeoning internet, ran 50 feet of Ethernet cable to a set of sensors that returned the temperature of his hot tub.
Connecting vending machines, CD players and other devices to the internet so that users could check on their status or even manipulate was an early 1990s trend that would eventually develop into the IoT. These days, device manufacturers are constantly thinking about connectivity and the potential for interoperability. When computer science students at Carnegie Mellon University connected a Coke vending machine to the internet, they mostly focused on user-to-machine communication. By 1999, the concept of device-to-device communications was introduced at the World Economic Forum to great interest; from this point on, machine-to-machine (M2M) communications would later become a protocol along with machine-to-infrastructure.
IoT applications are not limited to telematics, smart wearables, or home automation; this tech space is being tapped by virtually all industries, from healthcare to factories, farms and whole cities, particularly those engaged in device manufacturing.
Why IoT Brings Big Changes
It is not easy to determine whether Big Data or the IoT came first; what is clear, however, is that connected devices are able to provide massive amounts of useful data that can be monitored and analyzed for the purpose of improving the prototyping and product development processes. The insight that can be gleaned from IoT devices is something that 20th century manufacturers could have only dreamed about; these days, designers can actually see how their products are performing in real-time.
How IoT Affects Product Prototyping
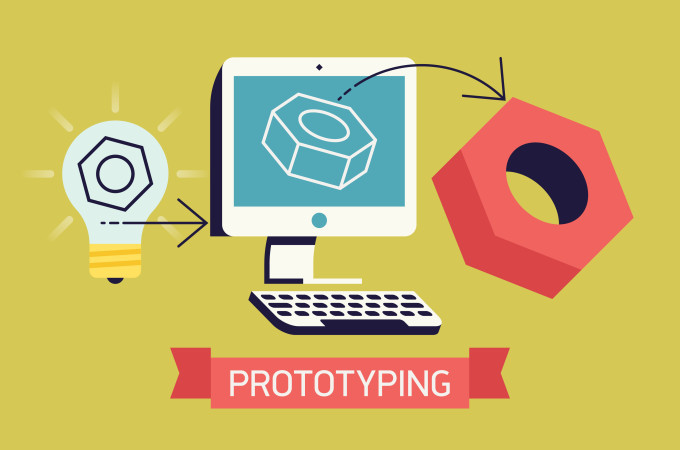
Original equipment manufacturers thrive on empirical data to advance their product development lifecycle. As a product designer, you would undoubtedly want to possess the intuition of Steve Jobs or Yuko Shimizu, the creator of Hello Kitty, but reality prompts you to rely on data to see how your creations, particularly your prototypes, are performing.
What the IoT offers with regard to prototyping is access to empirical data collected by means of sensors, cameras and interfaces. The IoT is not a silver bullet for the very first stage of prototyping, which will always require research, development, engineering, design, and fabrication; however, once the product is ready for testing, real-time data acquisition will make all the difference.
Similar to the historic Coke machine connected by Carnegie Mellon University students, Coca-Cola put its Freestyle vending machines on the IoT during the testing phase; these days, however, the soft drink giant continues to collect valuable data that goes far beyond the functionality of these machines. Coca-Cola has been able to see that Freestyle machines on college campuses are quite busy just before certain television programming comes on the air.
The days of expensive testing, intensive focus groups, a and learning from trial and error are being eliminated from prototyping thanks to IoT, and the decisions that need to be made before products hit the market can be formulated a lot faster.
How IoT Changes Research and Development
When Nabisco developed the curious “cheese in a spray can” product known as Easy Cheese in the 1970s, the label included a toll-free along with an invitation for consumers to call and report issues or to simply provide their thoughts about the product. Most of the calls received by Nabisco were complaints about the cheese spread failing to flow out of the can, and this is pretty much what the company expected since it needed to follow up on the product lifecycle management of Easy Cheese.
It is easy to imagine that the prototyping of Easy Cheese may have involved various kitchen and picnic mishaps of cheese flying all over the place or cans succumbing to excessive pressurization. Calls from customers to the 800-number provided by Nabisco were probably tedious and expensive to manage since they also required the mailing of certificates to replace the faulty cans, not to mention enticing consumers to send in their cans to figure out what may have happened, but this was all necessary R&D for the company.
The IoT makes it easier for manufacturers to monitor performance of their products in the field; any issues can be detected on the spot and solutions can be formulated before they become major issues. Moreover, the data gathered from products that are launched along with marketing campaigns can also be very valuable R&D information for future endeavors.
Switch from Product to Service Delivery
One of the new tenets of business created by the IoT and Big Data is that the information gathered from customer-product interactions is more valuable than the profits realized from the sales of products themselves.
The prospect of gathering valuable data is what has enabled social networks such as Facebook and Twitter to remain free services. Products connected to the IoT can be offered at lower prices and even for free if the data they are able to collect is more valuable for manufacturers.
With the above in mind, the business world is entering a paradigm shift whereby products are becoming instruments to deliver value through services. Microsoft Office 365 is a good example in this regard; this has been the profit leader for the software giant in recent years, and the company was able to acquire quite a few paid subscribers through free Windows 10 upgrades. The data that Microsoft has gleaned from the free Windows 10 product has allowed the company to fine-tune its Office 365 targeting efforts.
In the future, we may even see HVAC-as-a-service; in this case, companies will sell temperature control to be achieved with devices installed based on the flow of IoT data received and on the decisions made to maximize profits.
Final Word
The data flow created by the IoT should be a win-win situation not only for manufacturers but also for consumers and all stakeholders involved. Comprehensive real-time information should always be analyzed with the intention of improving products, services and overall experience. The goal is not to slow down the pace of engineering; the goal should be to make the right engineering decisions based on valuable empirical data. Instead of going through the arduous and expensive process of trial-and-error, manufacturers should embrace the IoT starting at the prototype stage and throughout the product lifecycle management process.
Additionally, check out this article by G2 Crowd which has in-depth information and analysis on the Internet of Things and its future, including how the IoT market is projected to reach a staggering $8.9 trillion by 2020.